To investigate an accident, try this four-point approach
- C P Prasanth
- Jul 4, 2020
- 2 min read
Updated: Oct 24, 2020
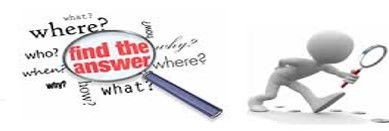
These instructions are a systematic approach to analyzing an accident. They’ll help you make sure you’re covering all the bases so you can learn from what’s happened and take the right steps to prevent it from happening again.
You may also find the attached “Accident analysis worksheet” useful. Fill out a worksheet each time you are investigating an incident. The worksheet will help you answer key questions about the incident and walk you through your investigation.
1. Collect data.
To begin with, you’ll want to find out some basic information about what happened, and then you’ll want to probe deeper.
Talk to witnesses. Besides the injured employee, others directly involved such as co-workers and the supervisor often can be good sources. Ask:
What type of injury occurred? Was it an accident? Body part injured?
What type of treatment was received? Physician? Hospital? Clinic?
Was there lost time from work? Number of days?
What happened and how did it happen? Was any equipment damaged?
What caused the incident? Why did it happen?
What could be done to prevent recurrence? By whom? When?
Was the employee violating safety regulations or specific instruction?
What other concerns do you have about this injury?
Help witnesses think through what they observed about the incident, otherwise you’ll probably get only a small portion of what they really know about it.
Ideally, accidents should be investigated right away. If an emergency makes that impractical, then do it as soon as you can while the facts are still clear to those involved, witnesses haven’t influenced one another thoughts, and the physical conditions haven’t been disrupted.
Review maintenance and training records. This may help you determine whether the accident was a result of an employee’s unsafe act or an equipment failure.
2. Identify the causes.
Accident investigation looks at four possible causes:
A. Equipment:
Is it working properly?
Are the guards and other safety precautions present and functioning?
B. At-risk behaviors:
Were there procedures not implemented?
Are safety procedures routinely enforced?
Was the employee working alone?
Was the employee out of sight from co-workers?
C. Personnel:
Was the employee properly trained for this particular job?
What shift and how long was the employee’s shift?
Can the employee read the language on warnings?
Was the employee wearing PPE?
D. Environment:
Was the work area properly lit?
Were work surfaces free of clutter and distraction?
Was noise an issue? Chemicals? Dust?
Was space sufficient to do the task?
Was the floor free of clutter?
3. Analyze the findings.
Examine the facts and observations, and be conscious of what’s missing.
Your analysis should distinguish between immediate causes and underlying causes. An immediate cause maybe an unsafe condition like a mechanical failure such as a broken rung on a ladder. Or it could be an unsafe action by an employee such as running instead of walking. The underlying cause could be poor machine maintenance, a missing guard, a crowded work area, lack of training or supervision.
4. Develop a plan for corrective action.
The plan should mirror the results you got from your analysis.
Make recommendations for each of the possible causes identified. After this investigation, for instance, you may suggest changes to machinery, work procedures, employee training, safety process or personnel.
Commentaires